Pump Maintenance and Repair Training: An Introduction
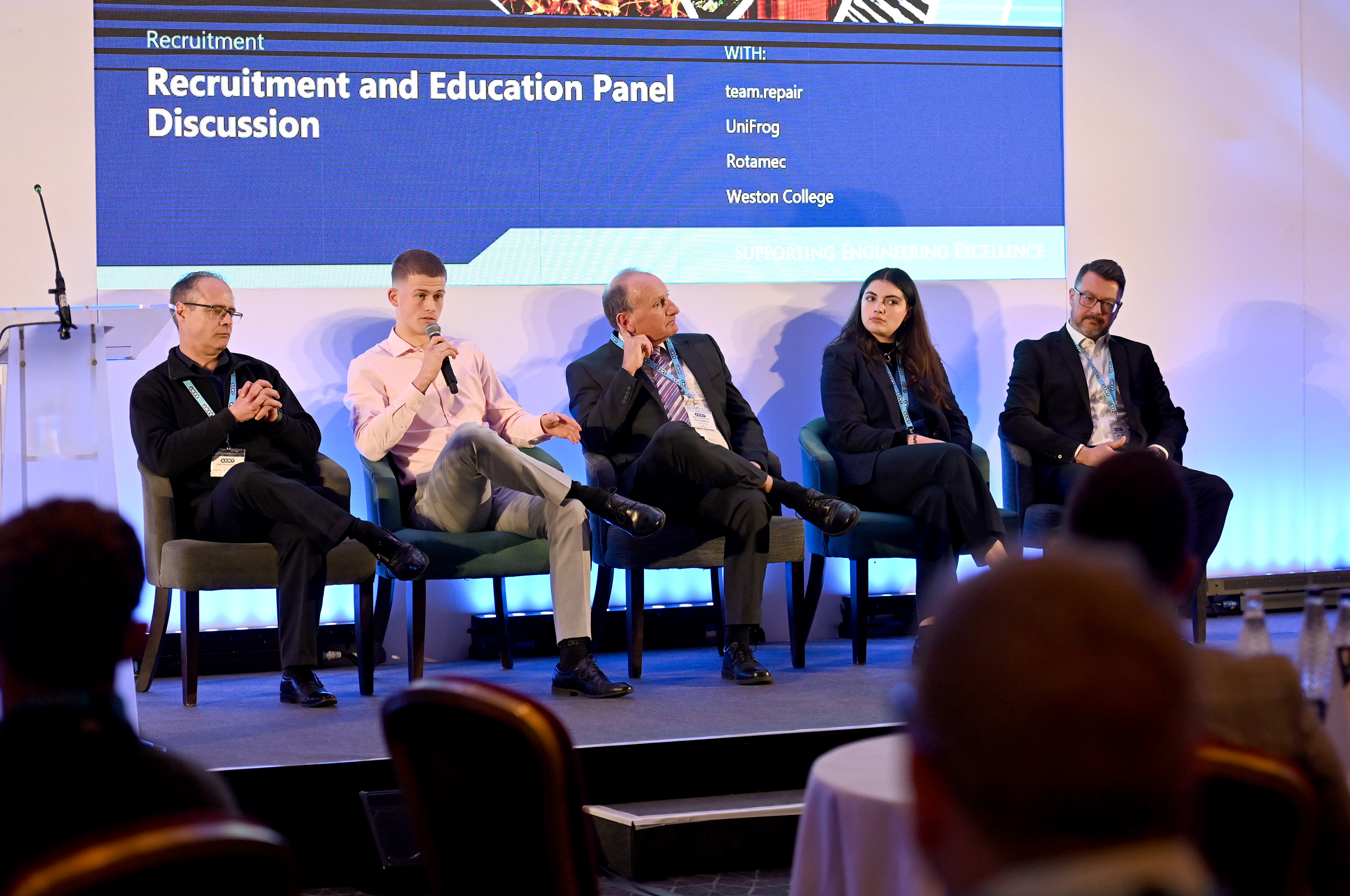
To book onto the full course contact the BPMA and mention you are a member of the AEMT for a discount on 0121 601 6691 or email admin.elearning@bpma.org.uk.
Overview of BPMA and the Pump Industry
- Gary’s Background: Over 40 years in the pump industry, spanning roles from fieldwork to management and marketing. He has been with BPMA since 2018, focusing on regulations, standards, and training.
- UK Market Size: The pump market in the UK is valued at approximately $1.3 billion, including pump parts.
- BPMA Training Programmes:
- Courses range from e-learning to advanced face-to-face sessions.
- Topics include pump fundamentals, selection, testing, system design, and energy audits.
- All courses are accredited for Continuing Professional Development (CPD).
Pump Repair Training Course
General Overview:
- Designed with input from industry experts, including leading manufacturers and suppliers.
- Incorporates hands-on learning with interactive models and real-world examples.
- Aims to cover all aspects of pump repair, from health and safety to advanced troubleshooting.
Day One Content:
-
Health and Safety:
- Workshop safety protocols, risk assessments, and confined space training.
- Use of appropriate tools, safety signs, and environmental compliance.
-
Pump Basics:
- Types of pumps: positive displacement and rotodynamic.
- Key components: shafts, impellers, casings, seals, and bearings.
- Materials used in pumps, tailored to application-specific needs.
-
Mechanical Seals and Motors:
- Identifying wear patterns, heat damage, and chipping.
- Motor specifications, efficiency ratings (IE1 to IE5), starting methods, and maintenance plans.
-
Bearings:
- Diagnosing common failures (e.g., flaking, scoring, corrosion).
- Importance of using genuine bearings for reliability and warranty compliance.
-
Repair Practices:
- Using genuine spares for lowest cost of ownership and OEM compliance.
- Focus on restoring pumps to manufacturer specifications for optimal efficiency.
Day Two Content:
-
Energy and Efficiency:
- Understanding when to use variable speed drives (VSDs) for energy savings.
- Identifying opportunities for replacing old, inefficient systems.
-
Advanced Troubleshooting:
- Cavitation, alignment, vibration issues, and system design flaws.
- Identifying causes of pump failure related to operating conditions and system changes.
-
Specialised Equipment:
- Coverage of specific pump types: diaphragm, sewage, booster sets, and submersibles.
- Training on test rigs and demo units provided by manufacturers.
-
Maintenance and Audits:
- Preventive maintenance schedules (weekly to yearly).
- Conducting energy audits to identify savings for customers.
-
Practical Components:
- Participants strip down and rebuild various pump models.
- Hands-on assessment of mechanical seals, elastomers, and other components.
Key Takeaways from the Course
-
Best Practices:
- Adhere to health and safety standards.
- Use genuine parts for repairs to ensure reliability and maintain warranties.
- Identify energy-saving opportunities and offer impartial advice to clients.
-
Comprehensive Training:
- Covers the complete lifecycle of pump systems, including auxiliary equipment like drives and controls.
- Ensures participants can deliver high-quality repairs and installations.