Bearings Designed To Last and Protect

Steve Bacon, Sales Director at Bearings and Drives Limited, shares an insight into the latest innovative technologies in operational efficiency to achieve new competitive advantages.
With a higher performance than traditional steel bearings, hybrid bearings are a combination of steel or stainless-steel rings used in conjunction with silicon nitride ceramic balls. As new technologies emerge, rolling elements (ceramic balls) of the highest quality, which on some occasions can take up to 60 days to manufacture, can be up to 58% lighter, four times smoother and have a 70% reduced thermal expansivity which can typically run at operating temperatures between 14-47°C lower than standard steel bearings. A combination of those pioneering properties can heighten efficiency, ensure that the bearings are less prone to the effects of contamination and corrosion, and have a greater intolerance to heat.
When taking into consideration the reasoning behind bearing failures, electrical currents are an increasing problem. The CeramicSpeed Insulate range includes custom-made ball bearings with a guarantee against damage caused by stray currents. The nonconductive ceramic balls, with an insulating capacity of at least 15kV/ mm, are ideal for use in electrical motors, generators and other applications where the passage of electrical currents must be avoided, offering significant advantages in terms of performance and durability over aluminium oxide coated bearings which are often offered as an alternative in these applications. Another important factor is the large energy savings that they deliver – up to 70%.
ELECTRICAL PROPERTIES
Issues caused by stray currents are often seen in systems run by frequency converters; however, other systems are also facing the problem. In an electric motor, a potential between the rotor and the stator can be induced by capacitive coupling or by frictional charging from a belt. Discharging will then happen through the bearings of the motor. This electrical current can damage the runways of the bearing rings, the balls and the grease in the bearing.
The current can take different paths in the motor depending on the origin of the induced voltages; if the voltages are created due to asymmetries inside the motor, the currents will circulate, as shown to the left in Figure 1. If the voltages are induced due to external factors such as a frequency converter, the current will flow from the axle to the housing in both bearings, as shown to the right in Figure 1.
A widely used step in order to prevent bearing currents is to apply an insulating coating on the outside of one of the bearing rings. The coating typically consists of a thin layer of aluminium oxide. An alternative, however, is to use a hybrid bearing such as the CeramicSpeed Insulate, where the balls themselves are insulating as they are made of silicon nitride instead of steel. Other protection methods are shaft grounding rings and ceramic coatings on the motor housing or the shaft.
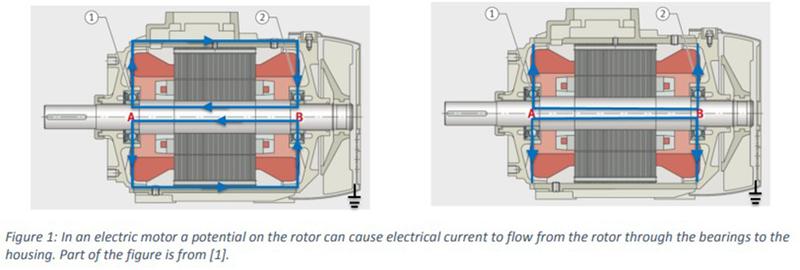
HYBRID BEARINGS VS. INSULATED COATING
High DC voltages can cause the insulating material to break down electrically, resulting in sparks/large currents running through the material – also described as the dielectric strength of the material. The DCcurrents that flow before a dielectric breakdown are so small that they are irrelevant.
In a coated bearing, both the oil film and the coating can break down. In the case of a DC voltage, the coating determines the breakdown voltage as the coating is much thicker than the oil. For coatings of 100μm, the breakdown voltage will be 1.3kV. At voltages below this value, the coating protects against DC currents.
For the hybrid bearing, however, the air between the bearing rings will break down before the balls. The thickness of the air is determined by the size of the bearing. A 5 mm air gap (6005 bearings) will break down at 5kV, and a 28mm air gap (6330 bearings) at 28kV. The breakdown voltage of a hybrid bearing will, therefore, increase with the increasing bearing size, while the breakdown strength of a coated bearing stays the same for all bearing sizes.
If a breakdown takes place in a coated bearing, the current will go through the balls and hence damage crucial parts of the bearing. If a breakdown happens in a hybrid bearing, the current will run through the air at the edge of the bearing and will not affect the performance of the bearing.
In the case of AC voltages, the picture changes completely for the coated bearing. Now it is not the thickness of the insulation layer which is most important but rather the area of contact between conductor and insulator. The contact area determines the capacitance and, hence, the impedance (the AC-equivalent to resistance). The contact area between the balls and the bearing rings is much smaller than the contact area between the coating and the rings. The impedance of the oil film is therefore much larger than the impedance of the coating. This means that almost the entire voltage drop over the bearing happens over the oil film. The dielectric breakdown will therefore happen in the oil film and not the coating. The coating will not prevent AC currents but only limit the amount of current through the bearing due to its resistivity. When using a frequency converter, frequencies at 0.5MHz have been measured. The impedance of the coating will, in this case, only be a few ohms and explains why large currents are able to flow in the event of an electrical breakdown of the oil film.
A hybrid bearing does not suffer under high-frequency AC fields as the balls are not conducting. Even at 0.5MHz frequencies, the impedance of a 6316 hybrid bearing is estimated to be 11kΩ compared to 18Ω for a similar coated bearing.
As the hybrid bearings will not be damaged at either large DC or AC voltages, CeramicSpeed offers a no-risk guarantee against bearing damage due to current through the bearing.
END-USER BENEFITS
While cost can often be a significant factor when making the switch from traditional to hybrid bearings, the additional expense of hybrid bearings, in particular, is certainly not relevant to each and every bearing application. Many maintenance engineers will have experienced at least one application where repeated and frequent bearing failures have led to regular loss of production, increased maintenance costs, and probable damage to other machine components. If bearings are failing on a regular basis, it is important to consider why. Could it be temperature issues, corrosion, contamination, grease problems or a combination of those factors? With new technological advancements, there could be a solution to aid the reduction of bearing failure downtime – whether it’s an off-the-shelf product or a bearing designed to suit very specific individual needs.
As new technologies emerge, not only can the lifespan of bearings be increased by an approximate factor of nine times, but the potential to increase production and make significant cost savings in reduced downtime is unlocked