Electric motors and the reliability journey
By adopting a circular journey, or a 'reliability journey', businesses can become more efficient in how they handle their electric motors. The approach helps drive the reduction of emissions and waste, supports the optimisation of energy efficiency and contributes to efforts to meet both CSR goals and performance KPIs.
CONDITION MONITORING
The first step in the reliability journey is condition monitoring. ERIKS' reliability platform leverages sensors that collect data on vibration, temperature, and other critical parameters in real time. This data is analysed using smart algorithms, which suggest potential causes and solutions with actionable insights. Data collected can then provide a complete view of both current and historical motor conditions, maintenance history, and identified maintainable items. With these insights, businesses can perform early fault detection, implement predictive maintenance strategies, and ensure compliance with operational standards. This approach reduces unplanned downtime and helps optimise the performance of critical assets.
ASSESSMENT
Once the condition monitoring tools indicate action needs to be taken, the next step on the reliability journey is the assessment phase. ERIKS can provide an independent assessment of a motor and advise whether to repair, replace or even upgrade. Working with a company with the know-how and resources for all these options, means organisations are not forced down one avenue; instead, the context of their situation can be used to help make an informed decision. For instance, if the turnaround is critical, then it might be that ERIKS can get the repair done and also source and supply a spare unit that the customer can store to prevent downtime on the next occasion.
Once a plan of action is agreed on, the ERIKS field services team swings into action. The company has significant flexibility when it comes to capacity and workforce, and if a customer has an emergency, then the whole network can be brought to bear upon it. For example, ERIKS recently came to the assistance of a customer that had experienced a critical failure by pulling in extra capacity from the network and implementing a shift pattern that meant a motor could be worked on 24 hours a day until it was ready to be returned. It takes a specialist with a certain size and scale to be able to do this.
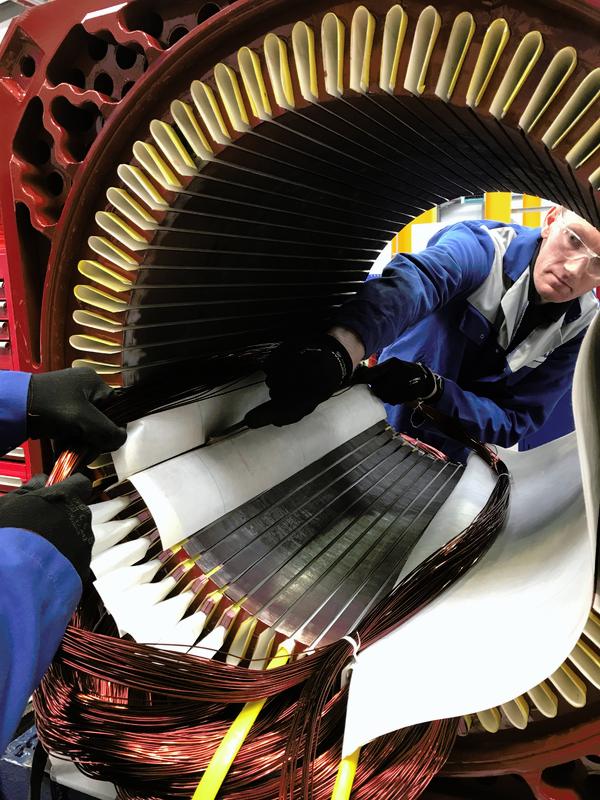
REPAIR
Following the assessment phase and the motor's arrival at an ERIKS workshop, the next phase in the reliability journey is the repair itself. As mentioned above, the logistics of getting a motor off-site and to the repair facility are handled by the field services team, but when it comes to mechanical engineering, ERIKS has engineers ready to carry out both standard repairs and rewinds as well as specialist services. Among these specialist services for DC motors are the in-house machining for commutator skimming and under cutting and commutator and slip ring repair and manufacturing.
While reliability is a broad term and can mean different things to different people, ERIKS believes that the quality of their repair work significantly impacts the long-term reliability of the motor. From the quality of the inspection of the motor to the materials used in its repair to the experience of the engineers working on the equipment, all of these factors help ensure that a repaired motor performs as required as opposed to failing again after just six months.
Reliability is a circular journey with all aspects leading to or impacting others. As with circular economy thinking, approaching electric motors with an overall reliability mindset leads to sustainability and environmental advantages. For example, more than 90% of the replaced parts in a motor are typically recycled, and with energy consumption and efficiency all being hugely important, the electric motor reliability journey enables continual improvement.
Another advantage for customers is the consistency of the standard of repair that ERIKS delivers across its network. ERIKS can handle the entire motor in-house repair. This approach means that the quality of repair is easier to manage, and lead times can be reduced.
TESTING
Testing is a crucial part of the reliability journey, and ERIKS tests every single repair at predefined stages. In many instances, customers can witness the testing for bigger units as part of their quality procedures. As well as dynamic balancing, the testing that ERIKS can offer includes partial discharge, Tan delta, insulation resistance, polarisation index, surge testing and IMCA broken rotor bar detection.
As part of its cradle-to-grave approach following the repair and testing, ERIKS is able to transport a motor back to the site and install and commission it, using its laser alignment tools to ensure the unit is correctly fitted and running as needed.
All ERIKS sites are certified to ISO9001 and ISO45001 and the company is a member of both EASA (Electrical Apparatus Service Association) and the AEMT (Association of Electrical and Mechanical Trades). ATEX motors can also be repaired.
CONTINUAL IMPROVEMENT
For larger customers all the aspects of the electric motor reliability journey can be handled through an ongoing framework agreement. With the continual improvement advantages such an agreement offers these are becoming increasingly popular. Plus, working with a supplier on an ongoing basis allows customer knowledge to be built up, allowing for a move away from a firefighting approach to more of a planned maintenance regime regarding electric motors.
With a much closer understanding of a customer's system, the opportunity arises to optimise the asset's performance, availability, and reliability. Frequent access to a given site makes improving asset performance easier. A single motor's reliability is not isolated to an assessment of its vibration, temperature, and noise data; it also involves the performance of the whole process – assessing perhaps if one piece of equipment is heavily damped and causing continual failures, for example. This performance optimisation can benefit customers by reducing energy costs and carbon emissions tax liability. Constant monitoring, coupled with the framework agreement style approach, allows root cause analysis of a customer's system to be carried out, which can identify assets for planned maintenance. This philosophy negates the headaches of catastrophic failure, which brings lost production and potential health and safety concerns.
There are other benefits of a framework agreement relationship. Terms and conditions are all well documented, as are Key Performance Indicators (KPIs). More importantly a Service Level Agreement (SLA) can ensure that the customer has the support they need (which may be a 24/7 emergency response) to give them peace of mind.
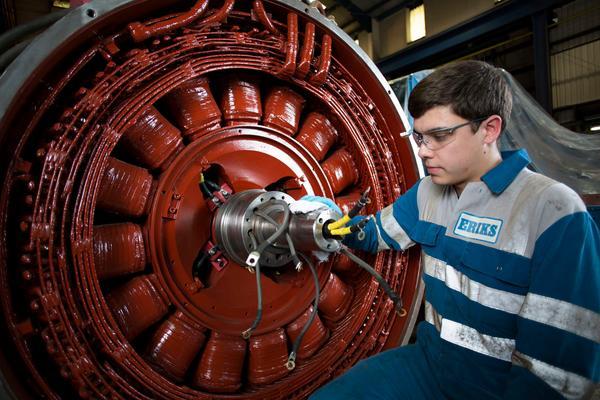
THE COMPLETED JOURNEY
With asset condition monitoring in place, we arrive back where we started our reliability journey. From the benefits of the various points of the journey, at a minimum, a motor is repaired and returned in 'as new' condition and if a partnership-style working arrangement is in place, the performance and availability of systems can be optimised from all angles, including energy use.
The circular reliability journey is one of continuous improvement using condition monitoring data to plan when the best time is to repair or refurbish a motor and then engaging with a partner with the logistics, the repair, the testing and the re-installation all handled for you. If a framework agreement is the right solution, then this can provide the added benefits of assessing an entire system and then reaping the benefits of improved performance and availability.
------------------
This article appeared in Renew magazine. To read more or request your personal digital or print edition of Renew, click here.