Electronics repair: Busting the myths
Our dependence on electronics in some of the most critical industries, such as defence, automotive, aviation, rail, energy and semiconductor manufacturing, has increased over the past 20 years. These sectors have transitioned from mechanical systems to highly automated and complex electronic setups. And while the technology boom has unlocked new possibilities, it has also created a throwaway society of e-waste, where companies are convinced it's cheaper and easier to replace equipment than repair it.
But there's a catch: more electronics means more reliance on original equipment manufacturers (OEMs). And with obsolescence now an unavoidable reality, businesses can be left stranded when parts are no longer in production, forcing them to undertake costly, unnecessary upgrades of entire systems or buy new machines just to stay afloat.
The global pandemic helped companies realise this, as they took a hard look at their maintenance budgets and realised just how much money was being wasted on unnecessary replacements.
Yet despite this shift, another challenge has become apparent. Skilled repair technicians who know how to troubleshoot and repair electronics are retiring or leaving the industry, while a lack of formal education options means that fewer younger engineers are being trained as replacements.
What's more, misinformation is widespread. Myths about the risks and viability of repair, particularly in electronic systems, have been growing, creating a stigma around the idea that repair is unreliable or impractical. But these myths couldn't be further from the truth, as we will show.
Repair isn't just possible. It's essential. And it's time to challenge outdated thinking and equip industries with the tools and knowledge to embrace a repair culture once again.
So here are 11 myths that have been spread widely, sometimes by OEMs keen to protect their sales revenue, that are simply not true and can lead to unnecessary waste and cost.
IT'S CHEAPER TO REPLACE THAN REPAIR
Simply put, in the longer term, it isn't. If you are replacing rather than repairing, the only thing you're doing is throwing money at spare parts, you're not learning anything. There could be some short-term gains, but you are likely to suffer long-term pains from this decision if you don't know why the parts are failing in the first place.
You need to think about how replacing is not necessarily helping your technical team to understand what's causing the faults. If you understand the cause, you can improve the machine or product's overall durability. Suppose you have in-house repair capabilities or a reliable partner who does. In that case, you may well be able to carry out a repair much faster than waiting for a spare, and you will inevitably also reduce costs. A PCB is typically 90% cheaper to repair than replace. So, for long-term gains, choose repair, not replace.
REPAIRING IS TOO SLOW AND DELAYS OPERATIONS
When something stops working, you need to have spare parts ready to go, but what happens to the faulty equipment or faulty circuit board that has been replaced? If you send it back to the manufacturer for repair, it might take six or even twelve months to have that system repaired and sent back to you. However, we have seen from working with many companies in the last 20 years that you can often repair circuit boards to the correct standard in just under ten minutes. So, it's not really a matter of time. You definitely need to have spare parts ready to go so that the machine can continue to operate. However, with the support of a local repair business, that repair can be turned around quickly. Plus, you're going to be reducing emissions and costs while improving your operational effectiveness.
REPAIRING OLD ELECTRONICS ISN'T WORTH IT
Many people ask, "It's outdated, why are we bothered about it?" Looks can be deceiving. Just because something looks old doesn't mean that it is outdated. For instance, programmes can last up to 50 years when you're talking about the defence sector. Yes, it might eventually look old, but that old piece of electronics is incredibly dependable. And it needs to be kept in operation for as long as possible. So, yes, it is definitely worth it.
In our experience, programmes will inevitably be extended. And if you haven't repaired the spare parts that you once had, they will have gone for good.
ONLY THE ORIGINAL MANUFACTURER CAN MAKE QUALITY REPAIRS
You might think that that was the case, but it's not. Many OEMs have lost the capability and capacity to repair, and we have seen OEMs bringing former employees from retirement to help them repair. Anyone with the proper training, the right troubleshooting equipment and the right rework systems can produce a very solid, high-quality repair. So, it's not just the OEMs that can do that.
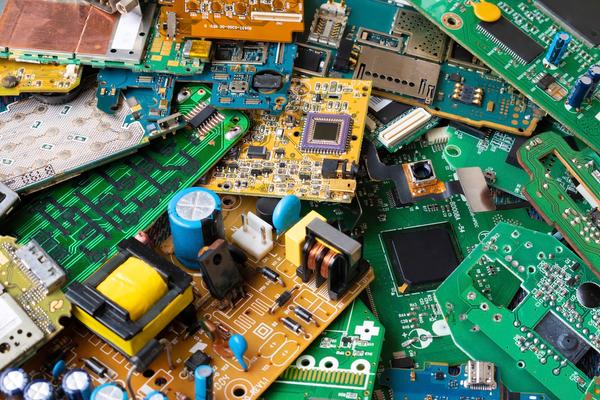
REPAIRING ELECTRONICS ISN'T ENVIRONMENTALLY FRIENDLY
I understand this point. There's a lot of greenwashing happening in our industry currently. People ignore sustainability by throwing away circuit boards and then assume that sustainability is all about having solar panels on their rooftops. But in reality, when you're repairing a circuit board, especially if you have a repair provider close to the point of use, you are reducing emissions significantly. You are removing a piece of hardware that required a lot of resources to be manufactured in the first place. If it is sent to landfill, it is waste. If you look to the OEM for a repair, you may be having that shipped halfway across the world in some cases. If the OEM doesn't have a very good troubleshooting process, they may be unable to trace the fault, and in many industries, if you have no fault found, eventually, that piece of equipment gets scrapped, which is madness. So, it's all about having the capability to do as much troubleshooting as possible close to the point of use.
REPAIRS WON'T LAST AS LONG AS REPLACEMENTS
People tend to ignore the fact that circuit boards have weaknesses. They all do. So, if you are replacing like for like, guess what, the same weaknesses that were present on day one when you bought the system, will be there again in time, causing the fault again. Durability is not related to the age of the PCB, but to how it's being maintained, how it's being operated and the quality of the components it was manufactured with.
I can mention one case involving a Spanish train manufacturer with an ATC ECU card failing every two months, and they didn't know what was happening. Replacing the cards did not resolve the issue. So, it was only when they invested in the right equipment, which happened to be the BoardMaster from ABI Electronics, that they identified the real issue: a communication IC wasn't robust enough for that operation and was failing within two months. Once they had identified the problem and upgraded the design to a more robust communication IC, there were no more failures.
A well-carried-out repair that identifies and addresses the root cause of an issue can improve reliability. for that operation and was failing within two months. Once they had identified the problem and upgraded the design to a more robust communication IC, there were no more failures. A well-carried-out repair that identifies and addresses the root cause of an issue can improve reliability.
REPAIRING ELECTRONICS ISN'T SAFE
Of course, repairing electronics isn't safe if you don't know what you're doing. It's all about being trained, and this is very important. Anyone carrying out electronics repairs needs to understand how components work, they need to understand what to do when they don't work, and they need to know about all the different tools that they have at their disposal to execute the repair to the correct standard. There is an organisation called IPC where these standards are made available to anyone who wants to run professional repair operations. You can also find a range of training and materials online, such as those at repairdontwaste.com, where there is a 'learn' tab and the standards are available.
IT'S TOO HARD TO FIND REPLACEMENT PARTS
This is true in some cases. But it's all about planning and understanding what the alternative parts are as well. It's incredibly important that companies see repair as a first line of defence against obsolescence. If you're struggling to find parts, your obsolescence management system is not working properly, or you're thinking about obsolescence management too late. Repair and obsolescence management go hand-in-hand, and they should be implemented from the moment a project starts, when equipment is delivered. That's when you should be thinking about how repairs and managing obsolescence management will be covered.
REPAIRING ELECTRONICS DOESN'T IMPROVE PERFORMANCE
As mentioned earlier, with the Spanish train project, durability can be improved. You can improve the longevity of circuit boards and, as a result, the wider systems they are part of. If those systems can be kept in operation for longer by having their parts repaired and improved, the overall cost of ownership can be reduced.
REPAIRS DON'T MATTER IN A FAST-PACED INDUSTRY
This is something that we are hearing a lot; time is money. But as I mentioned earlier, if you or your repair partner have planned well, if you have a stock of spare parts, and if you have trained technicians and the right equipment, you can maintain that same inventory of spare parts independently and very quickly, rather than waiting months and paying a small fortune for repairs.
One of our customers, the Royal Bahrain Air Force, mentioned a piece of equipment having a fault. They had an idea what the fault was, but they were not sure, so they sent that piece of equipment back to the OEM in America. The OEM said it would take nine months to get the equipment back to them, and it would cost $15,000. Or, if they wanted the system turned around in six months, then there would be a premium on top. The Bahrain Air Force decided not to proceed with the repair and requested the return of the equipment. On the day it returned, they managed to locate a faulty capacitor that failed. A replacement capacitor was acquired in the local market and replaced on the board. And the overall cost was only $0.15. So, this went from $15,000 to $0.15, and the repair was carried out on the same day.
OLD ELECTRONICS ARE LESS ENERGY EFFICIENT
Recently, I was at the InnoTrans exhibition in Berlin, participating in one of the roundtables on circular economy and sustainability. After the event, I was approached by a procurement officer from a large European rail operator who said it's frustrating when you come to events like this, and the only thing you hear from OEMs is that in order to become sustainable and achieve net zero, you need to invest in the latest, most modern and most advanced piece of equipment. And that railway operator told me that this is madness. We really need the ability to keep the good equipment we already have going for as long as possible. Indeed, the most sustainable equipment is the equipment that already exists.
In many sectors, there is no money to buy the latest, most modern equipment. The rail operator is a huge operation with hundreds of trains transporting millions of passengers, but it's not a very lucrative business, so they are under pressure, and they are being told that they need to invest in the latest equipment in order to achieve sustainability. But this is not true. I believe that you need to keep what you have going for as long as possible, because many excellent innovations have been implemented in the last 15 to 20 years. And there's a lot of life left in them.
So, there you have it –11 myths about electronics repairs debunked. Repair isn't just a matter of fixing what's broken, it's about sustainability, cost savings, and independence from restrictive OEM practices. I encourage you to think about how to implement repair strategies in your operations, identify a suitable partner you can rely on for electronics repairs or building in-house repair capabilities, train technicians and plan for obsolescence. This isn't just good business; it's essential for a sustainable future.
------------------
This article appeared in Renew magazine. To read more or request your personal digital or print edition of Renew, click here.