Houghton International Invests in New Dedicated Wind Turbine Repair Facility
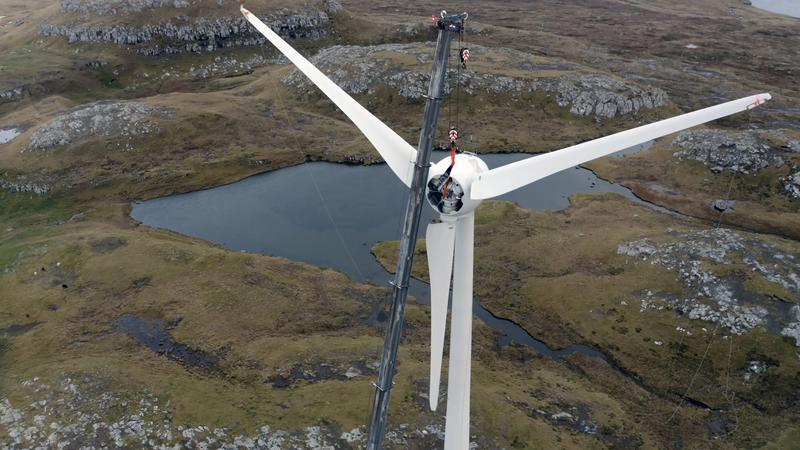
The company recently completed a repair and life-extension project on an Enercon direct drive wind turbine in the Faroe Islands – its second successful project on such equipment – and expects a significant upturn in demand for its unique services in the coming years, driven by the world's need to generate clean energy and reduce the length of outages experienced by wind farm owners and operators when their turbines fail.
Michael Mitten, CEO of Houghton International, said: "We were a subcontractor on our first Enercon turbine repair project, but with this one, we were the primary contractor, leading the entire job. This included diagnosing the fault and specifying the solution, which included a marked improvement in the generator's insulation system and weatherproofing from the original design. We then managed safe dismantling and logistics, executing the whole repair and life extension project as well as reinstalling and commissioning the unit. This was all carried out under incredibly challenging conditions in the Faroe Island's volatile weather
environment."
Repairing and life-extending direct drive turbines, including upgrades to the original design, has taken roughly six months, which is far quicker than waiting for a new replacement that can take up to two years to be delivered. The new investment in creating a dedicated repair facility within the company's existing facility will reduce those lead times by roughly 20%, meaning asset owners can return their generators into service far quicker, generating clean energy and profits much faster.
Importantly, repairing rather than replacing is essentially a carbon-neutral process. All the original equipment is being reused, and what is not reused is fully recycled with only a small percentage of waste material, meaning far less energy is consumed and less harmful greenhouse gasses are produced via the repair process compared to manufacturing an entire new unit.