Reliability-Centred Services Cut Maintenance Costs
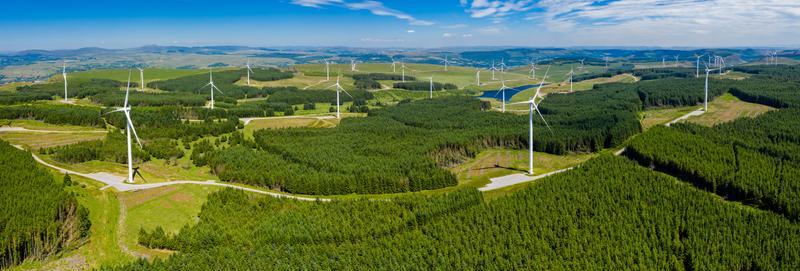
The risk landscape that industrial enterprises are navigating in 2023 is complex, volatile and distinctly lacking the one thing that almost every business craves – certainty.
As inflation cuts into margins and profits, budgets are being squeezed and efficiencies sought. For example, businesses are now, more than ever, looking to reduce unplanned asset downtime that has a negative effect on both productivity and output.
In very simple terms, reliability-centred services are all about increasing uptime. To maximise uptime, customers should consider a range of recovery and/ or planned data and advisory services designed to meet their unique service and maintenance needs with the key objective of preventing downtime.
The financials involved with unplanned downtime are serious – it accounts for up to 20% of the overall cost of a facility’s operation. According to ABB calculations, in the food and beverage sector, for example, downtime can cost from $4,000 - $30,000 per hour, which becomes a very substantial amount when you consider that up to 12 hours can be lost in a single incident if cleanup operations are required. Paper producers, meanwhile, lose up to $25,000 every hour when a key asset breaks down, with the steel industry averaging around $300,000 in losses per critical machine failure.
As well as the direct costs associated with wasted materials, replacement parts, labour, cleanups, loss of production, logistics disruption and restarting processes, downtime also presents businesses with several indirect costs. These include reputational damage, health and safety risks, loss of team morale, insurance premium rises and inventory management shakeups.
INVESTING IN RELIABILITY
Having spent 17 years inside ABB, I have seen first hand how the industrial technology landscape has evolved as well as how our industry is looking at new operating models, both with the aim of maximising uptime.
Technology is enhancing the value of reliability-centred services. Digital solutions such as augmented reality (AR) are unlocking opportunities to collaborate with customers virtually through remote installation, commissioning and general support. Service engineers can carry out remote assessments on demand, providing speedier resolutions that help to reduce downtime, costs and health and safety risks.
Meanwhile, connecting assets and tracking their performance is enabling a shift towards predictive maintenance informed by data. This triggers early interventions and helps to prevent failures from occurring. This approach, also known as condition-based monitoring, is helping to transform maintenance operations across a range of industrial sectors.
Last year in Guangdong, China, ABB digitally connected 34 critical motors of various pumps, fans and mixers at the Zhuhai power plant, a two-unit 600MW coal-fired power plant that produces 3.9 billion kWh of electricity annually. The site’s desulfurisation plant had experienced unplanned downtime due to motor failures, resulting in power interruptions for the city of Zhuhai. The condition monitoring solution enables the customer to monitor operational variables and health indicators remotely, avoiding this risk by collecting data on key parameters from the motors. This allows early intervention when needed and has significantly increased uptime, saved costs and increased employee safety by reducing the need to carry out manual monitoring work in high-risk areas.
The latest technologies and retrofitting capabilities are also helping companies deal with growing cost pressures. Upgrading ageing assets with the new functionality and features can often save them from being scrapped or replaced while also helping to maintain continuity of operations.
This was the case during our planned maintenance services schedule with Enefit Green, the largest wind energy producer in the Baltics. Across its portfolio, ABB ACS800 converters are utilised in 24 wind turbines at the company’s Aulepa and Aseri wind farms. Rather than purchase new converters, it replaced the old ACS800 units with reconditioned ones – as well as maximising reliability and extending lifetime; the reconditioning option has enabled Enefit to cut emissions by 79% compared to buying brand-new parts.
MOVING UP THE RELIABILITY LADDER
In many ways, proactive reliability-centred services represent an insurance-style model that lowers or removes the risk of industrial operations away from the business and onto the service provider. The goal should be to “climb the reliability ladder” – moving from a high-risk reactive maintenance strategy (where you fix equipment only when it fails), to a moderate-risk conditionbased maintenance strategy (where you fix issues before they result in failure), to ultimately a low-risk long-term outcomebased service agreement (where a service provider guarantees an outcome, for example uptime or energy savings).
Each step up the ladder is also highly cost-effective – according to the US Department of Energy (DOE), a conditionbased maintenance strategy, including condition-based services, provides 40% savings over a reactive maintenance strategy, for example. Against a backdrop of inflation, budget squeezes and productivity challenges, the ability of industrial enterprises to maximise uptime by carrying out cost-effective, data-driven maintenance schedules is crucial to the ongoing viability and sustainability of operations.
In the middle step of the ladder, we find examples such as Ruchira Papers – an Indian manufacturer that produces printing, writing, and kraft paper from agricultural waste materials. Even though local service suppliers were fixing failing equipment, the facility was still experiencing four to five unplanned downtimes a year due to a lack of a solid maintenance strategy on drive-controlled applications. The company decided to enter into a long-term condition-based agreement, where ABB has now taken full responsibility for the servicing of 55 drives throughout their whole life cycle. The agreement includes preventive maintenance, on-site support during interruptions, technical remote support, spare parts inventory management, reconditioning, and modernisation services or replacement. Since the agreement started two years ago, the facility’s uptime has increased by 13% up to 94.8% – giving Ruchira Papers peace of mind for it to focus on its core competence.
The final step of the ladder is a fully outcome-based maintenance model, where a business only pays for the achieved outcomes, rather than purchasing individual products or maintenance and repair activities. This shifts all the risk onto the maintenance service provider, and therefore connectivity is key. Statkraft installed two new ABB synchronous condensers in Liverpool, England. The system helps ensure that the UK grid remains stable as it integrates more variable sources of energy – like wind and solar. To ensure that this vital system is available around the clock, ABB and Statkraft entered a 10-year service agreement that will ensure uptime by providing a full range of planned and quick response maintenance services. These include digital condition monitoring that allows remote operators to analyse real-time data to plan corrective actions before issues occur – ensuring high system reliability and uptime.
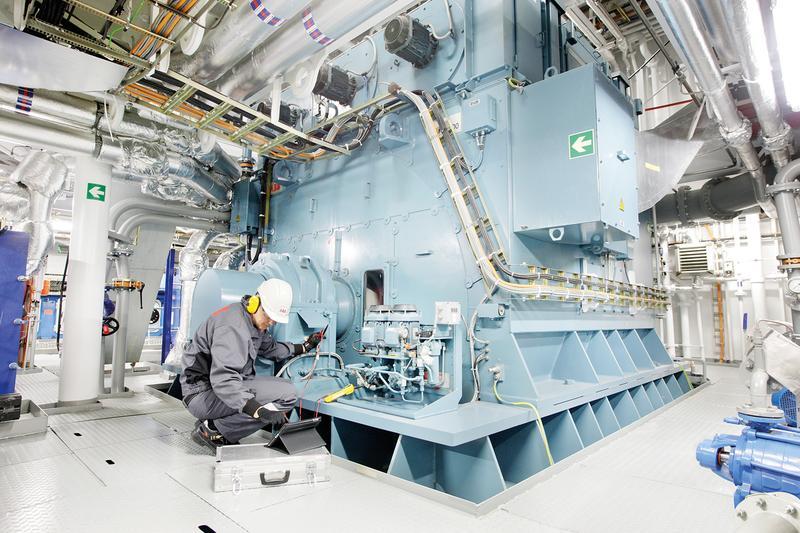
TOWARDS A MORE RELIABLE FUTURE
An additional benefit of investing in reliability is energy savings. A further DOE study showed that businesses can achieve 20% savings in annual energy costs by shifting to a preventive maintenance strategy that uses the latest technology to extend the life cycle of their equipment.
Digitalising equipment enables it to be used in the most energy efficient way. For example, we are working with CERN, the world’s leading particle physics laboratory, to digitalise assets in its cooling and ventilation systems for condition monitoring purposes. Motors used to power pumps, fans, compressors and cooling towers – which account for about 20% of CERN’s energy consumption – now relay data back to remote operators for them to optimise energy usage. The aim is to achieve an improvement of up to 15% in the energy efficiency of the cooling and ventilation systems.
As industrial processes become more complex, the risk of downtime is heightened as skills gaps widen and new generations of operatives come on board.
However, the maintenance and uptime burden does not need to fall entirely on inhouse teams.
Providers of reliability services are there to plug knowledge and labour gaps, provide rapid response support when needed, and help companies transition to better ways of monitoring critical assets. Whether it’s fulfilling a callout-style emergency response need or playing the role of a longerterm strategic partner to help transform approaches to maintenance, reliability services can be tailored to suit every requirement.
Indeed, by tapping into an established supply chain of expertise, such as that offered by ABB Motion Services, organisations can put some much-craved security, resilience and certainty back into their operations and remove some of the risks associated with downtime. From saving money to avoiding reputational damage, reliability services exist to futureproof industrial businesses.